Behavioral Safety
6 min readThe application of behavioral science has contributed greatly to improvements in safety. From behavior-based safety to safety leadership to developing a positive safety culture, the science of behavior has helped thousands of organizations improve safety performance.
Many organizations implement safety programs using elements of the science such as behavioral observations, feedback, and the reinforcement of safe behavior, but these only scratch the surface of how the science can help. Rather than limiting behavioral science to specific safety processes, organizations can reap the full benefit of science by applying these principles whenever making decisions that affect safety. Behavioral science provides evidence-based strategies for optimizing any and all safety systems that involve human behavior.
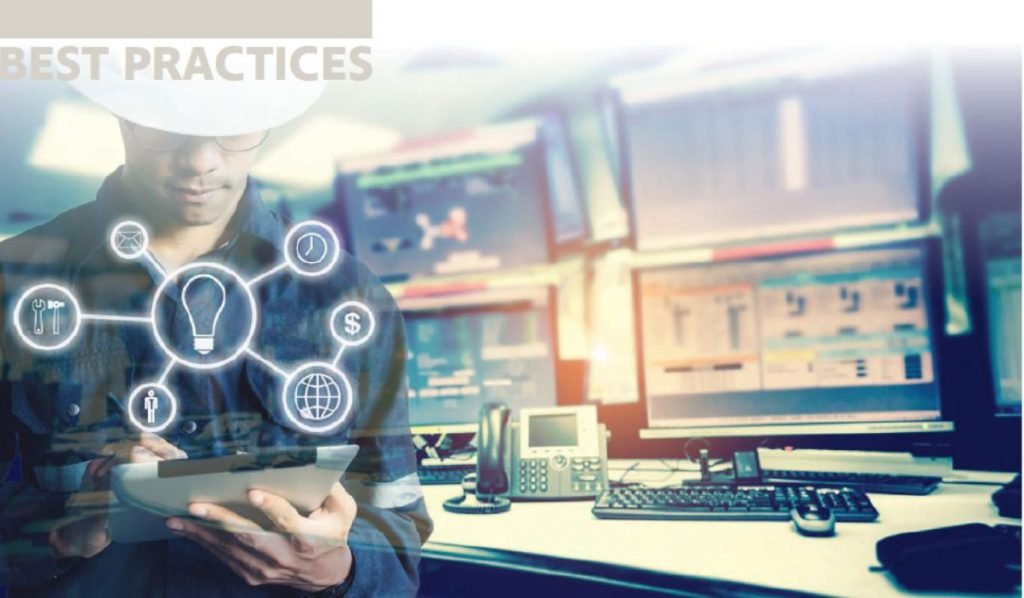
Today’s workplaces are in a constant state of change. New technologies, changing markets, and improvements in safety practice all require changes in behavior, at every level of the organization. Applying the science of behavior ensures rapid and sustained behavior change, yet often organizations do not use these tools and principles to make these necessary changes. Following are examples of new technologies and practices that should have improved safety, but wound up being less than effective because organizations did not apply behavioral science when implementing them.
- Transportation companies install cameras in vehicles to monitor driver behavior and reduce collisions, then find camera lenses tampered with (e.g., covered in petroleum jelly, cords cut or disabled in some way).
- Dangerous jobs previously performed by humans are now performed by robots and other computer-controlled devices, leaving humans to simply monitor the computers. Organizations repeatedly find those who should be monitoring the process are asleep on the job, even going so far as to build hidden beds for themselves.
- Process safety is introduced with training and fanfare, but over time the process checks and procedures are completed inconsistently, resulting in dangerous exposure.
- Organizations strongly encourage near-hit reporting for the purpose of organizational learning but find that only a few minor incidents are reported, and little organizational learning is accomplished.
- Hazard identification training results in a temporary increase in hazard reporting, which fades over time despite constant reminders from leaders to continually look for and report hazards.
- Senior leaders shift from lagging indicators to a dashboard of leading indicators to monitor safety performance, then discover that many leading indicator metrics are being pencil-whipped or inaccurately skewed to the positive.
What many organizations fail to realize is that these outcomes can be understood, predicted, and, most importantly, avoided by the application of behavioral science. Following are behavioral explanations for each of these scenarios and recommendations for how to maximize their desired impact.
” New technologies, changing markets, and improvements in safety practice all require changes in behavior, at every level of the organization.“
Sensors in Vehicles
Sensors can provide moment-by-moment data on the position and speed of vehicles, braking, and other indicators of driving performance. On the surface, this technology seems like a godsend in that it allows organizations to know how operators are driving when they are out of sight of supervision and provide feedback to improve safe driving behaviors. Unfortunately, the natural tendency in most organizations is to set up systems that alert management to driving exceptions, the things drivers do wrong. This leads to the use of more frequent negative feedback and discipline to manage behaviors. Not surprisingly, drivers view this technology as “big brother” and resist its use, even disable the technology to avoid negative consequences. Those who understand behavior scientifically know that anything that leads to more negative consequences will be resisted. To make such technology effective, it should be used to positively reinforce safe driving behaviors and improvements in those behaviors, in addition to providing feedback on at-risk driving behavior. The balance of consequences should heavily favor the positive. Any technology that leads to more positive reinforcement will be welcomed, not resisted.
Computer Monitoring
Monitoring computers is often boring work. When everything is running well (i.e., highly reliable) there are rarely issues to see and respond to. It is perfectly predictable that attention will drift. The technical term for this is extinction. There is nothing to reinforce the behavior of looking when everything is always working as it should be. If organizations need people to be diligent about monitoring, they must find ways to build in reinforcement. Rotating tasks that require high attention levels with standard monitoring tasks is another option. “If you design jobs that require employees to constantly monitor systems that rarely fail, you are designing jobs that will put people to sleep. To then punish people for falling asleep is unjust.”
Process Safety Behaviors
Many process safety behaviors are similar to the monitoring behaviors noted; they are designed to check and make sure nothing is wrong. Therefore, they are also susceptible to extinction. Other process safety behaviors such as communicating vital information and diligently following procedures are all designed to prevent low-probability events, making it all too easy for workers to skip them in favor of seemingly more pressing work (“It will be okay to skip this check just this once. I’ll do it tomorrow.”).
Again, this is perfectly predictable once you understand that the more immediate and certain consequences are, the more powerful they are. More pressing work is work with immediate and certain consequences, and, thus, will always be done before work with future, uncertain consequences. The solution lies in using this knowledge to build in more immediate and certain consequences for the process safety behaviors so they do not succumb to procrastination, thus leaving sites vulnerable.
Near-Hit Reporting
Despite communicating the desire for employees to report near-hits, most organizations inadvertently discourage reporting by how they react when a near hit is reported. In obvious cases, the use of discipline or termination sends a chilling message through an organization, reducing the tendency to report. Less obviously, time-consuming paperwork, uncomfortable interviews by managers and public sharing of the near-hit events all often serve to discourage people from reporting. Remember, reporting a near-hit, even without these kinds of consequences, is unpleasant for most people because it often requires admitting to having made a mistake. To increase reporting of meaningful near-hits, reporting must be positively reinforced and negative consequences minimized. This may mean building in anonymity or other compromises (e.g., reduced paperwork) that make learning from the near-hits easier or more likely. The bottom line: If people don’t report, no learning can take place.
Hazard Reporting
Many organizations have an increased focus on hazard identification and remediation because it is clear that the more hazards that get reported and eliminated, the safer the workplace. Again, reporting a hazard is a behavior that must be positively reinforced to be strengthened. Unfortunately, many organizations’ hazard remediation processes do little to positively reinforce reporting. Too often, employees state that reported hazards go into a black hole. Those reporting do not get feedback on what they have reported, and sometimes the hazards are not fixed for weeks or months, if ever. It doesn’t take many experiences like this for extinction to set in. People think, “Why to bother?” and stop reporting.
While the best reinforcer for reporting a hazard is to have that hazard remediated, employees understand that is not always immediately possible. Communication serves as a bridging reinforcer until the hazard can be taken care of. As long as people know why there is a delay (e.g., waiting on parts, necessary budget review) and are updated regularly, they will be willing to continue to look for and report hazards.
Managing With Leading Indicators
Managing safety with leading indicators is a huge step toward true preventive safety management. However, how those metrics are used matters. If managers know that bad numbers will lead to negative consequences from senior leadership, they will do what they can to avoid bad numbers. Senior leaders must learn to embrace and celebrate less-than-perfect numbers in safety because those numbers provide insight into what to do to improve. Rather than holding managers accountable for having good numbers, senior leaders should hold them accountable for careful analysis of what the numbers say about the current state of incident prevention, and for following through on corrective actions.
Conclusion
As these examples demonstrate, behavior change is an inevitable requirement of safety improvement, whether necessitated by technology, safety culture goals, or a more sophisticated understanding of risk.
The most cutting-edge technology will not help save lives if people do not use them properly.
Now more than ever, an even deeper understanding of behavior is required to improve safety performance. Organizations that learn how to apply the science to identify and analyze required behavior changes will be able to anticipate the inevitable behavioral challenges that new technology brings, and take steps to align organizational systems to accelerate and sustain those desired and needed behavior changes.